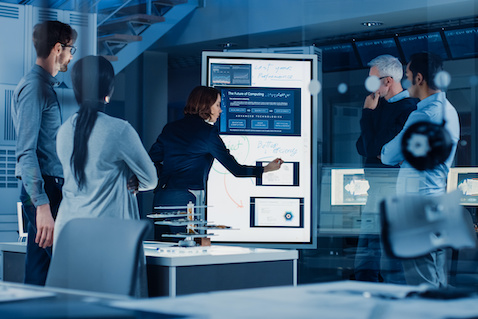
14 pomysłów na projekt rozwojowy dla Twojego zespołu
Kryzys to najlepszy moment dla zespołu, żeby wykazać swoją wartość, ale trzeba wyjść z inicjatywą.
Przez 15 lat moja firma przechodziła różne kryzysy. Były momenty prosperity i momenty trudne. Pamiętam kryzys 2009-2011 kiedy nasze źródła dochodów wysychały szybciej niż kałuże po letnim deszczu, a 6-cyfrowy debet na rachunku firmowym motywował do działania jak najlepszy energetyk.
Przed nami trudny czas, a ja nie tracę optymizmu. To czas dla odważnych, którzy zadbają o przyszłość i odpowiednio wcześnie wezmą sprawy w swoje ręce.
Jeżeli nie jesteś defetystą i masz poczucie, że kryzys to nie tylko zagrożenie, ale szansa dla Ciebie i dla Twojego zespołu, a Ty tylko potrzebujesz inspiracji – czytaj ten artykuł.
To wezwanie do działania. Bo działać trzeba. Rozważnie, ale odważnie!
Czas na Twój ruch.
Pierwszym krokiem była diagnoza
W latach 2016-2018 zbadałem motywację pracowników w projektach optymalizacyjnych. 220 zespołów rozwiązywało problemy jakości, wydajności lub naprawiało komunikację wewnętrzną w swoich fabrykach. Nie wszystkie projekty przełożyły się na pieniądze, ale te którym się udało, dały ponad 86.7 mln złotych rocznych oszczędności.
W pierwszej fazie, członkowie zespołów ocenili, które problemy są dla nich najważniejsze i wybrali te o największym potencjale dla firmy.
Oto 713 zidentyfikowanych problemów w 4 kategoriach:

56% problemów to MUDA
W najliczniejszej grupie wskazali 403 problemy, które wpływały na obniżenie efektywności procesów.
Były to:
- błędy jakościowe i “reworki” – 106 zespołów wskazało ten problem jako kluczowy i warty “przepracowania” na dalszym etapie projektu
- straty na oczekiwaniu w procesie – 65 zespołów
- zbędny transport – 54
- praca nie dodająca wartości – 52
- tzw. “8 MUDA” – czyli utrata potencjału fizycznego i intelektualnego pracowników – aż w 44
- nieterminowość – 29
- nadmierne przetwarzanie – 16
- nadmierne zapasy – 15
- nadprodukcja – 9
- przeciążenie procesów lub ludzi – 8
- niezrównoważenie – 5 zespołów.
26% w obszarze HR
183 zidentyfikowanych problemów znalazło się w kategorii HR – ponieważ występowały w obszarze personalnym.
Były to:
- niska jakość komunikacji i współpracy w zespole / pomiędzy nimi – 71 zespołów zdiagnozowało ten problem jako najważniejsze dla ich firmy wyzwanie
- obniżający się poziom motywacji pracowników – 58 zespołów
- zwiększającą się rotację – 36
- niewystarczające kompetencje nowych pracowników – 18 zespołów.
13% w TPM
91 zespołów wskazało problemu z utrzymaniem ciągłości działania za krytyczne dla swoich fabryk.
Należały do nich problemy związane z:
- rozruchem produkcji – ten problem zidentyfikowały 34 zespoły
- chronicznymi awariami – 24
- krótkimi przestojami i spowolnieniem operacji – 20
- oraz zmniejszoną wydajność – 13 wskazań zespołów.
Po diagnozie przyszedł czas
na wybór tematu projektu
Nie wszystkie problemy oparły się surowej ocenie zespołów i decydentów.
Na niektóre z nich uczestnicy nie mieli wpływu i musieli pozostawić nierozwiązane. Z niektórymi firmy poradziły sobie za pomocą innych środków, a w części istniało ryzyko zbyt wysokich nakładów i zbyt niskich korzyści.
Dlatego ekipy wybrały 3 obszary, w których spodziewane rozwiązanie problemu miało dostarczyć najwięcej wartości.
Były to:
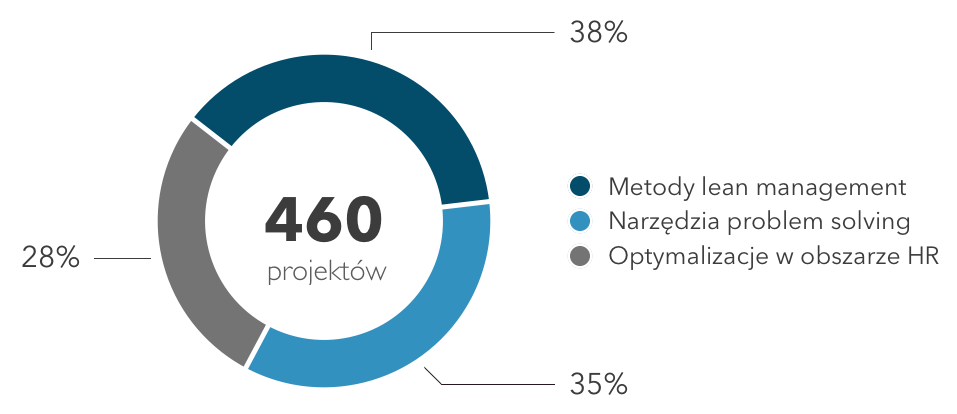
38% tematów dotyczyło wdrażania LEAN
173 zespoły zdecydowały się na rozpoczęcie projektu z obszaru lean manufacturing, których celem było eliminować straty i zwiększać efektywność procesów.
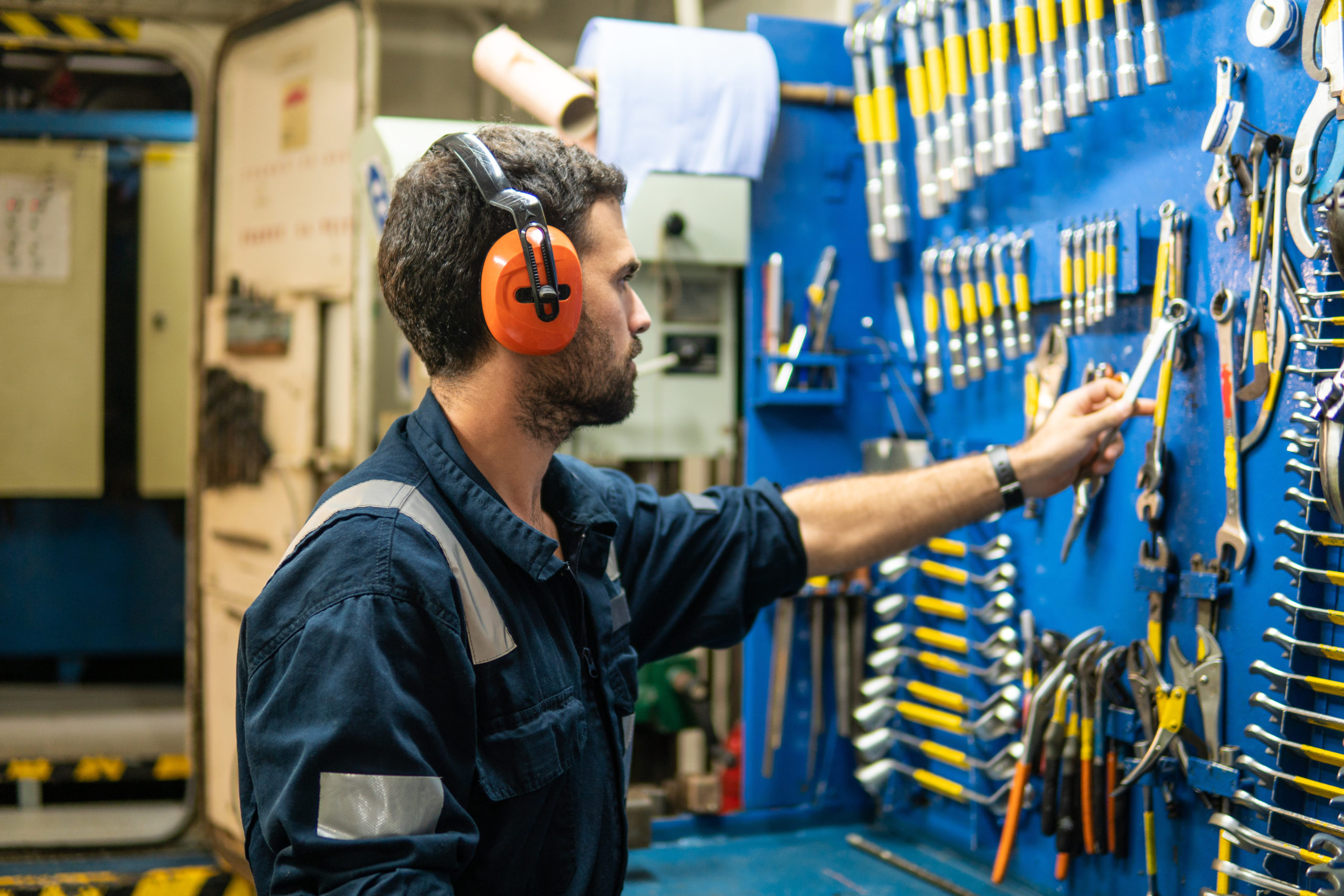
Zgodnie z metodą SMART zespoły zobowiązały się zaplanować i wdrożyć takie działania optymalizacyjne, dzięki którym, w określonym czasie poprawią się i utrzymają na oczekiwanym poziomie wybrane wskaźniki produktywności.
Aby ułatwić sobie pracę i nie stracić motywacji na samym początku – zespoły zwykle nie wskazywały docelowego poziomu KPI, ale widełki – maksymalnie oczekiwany poziom poprawy i minimalnie akceptowalny – dając tym samym szansę “wstrzelenia się w przedział”.
Wspólnie ustaliliśmy, że dla większości z nich liczyć się będzie nie perfekcja – ale ważny będzie postęp.
14 tematów do inspiracji
Spośród wszystkich projektów LEAN za najbardziej rokujące uznano 6 tematów:
- 5S i visual management – tego typu projekty wybrał 61 zespołów – muszę w tym miejscu dodać, że fabryki w których prowadziłem swoje badania i warsztaty, to dojrzałe zakłady produkcyjne, które wielokrotnie przechodziły przez projekty lean. Okazuje się, że 5S zawsze na topie.
- udoskonalenie aktualnego TPM – 37 zespołów, a wśród nich ponad 50% wdrożeń wiązało się z Autonomicznym maintenance – więcej na temat najważniejszych wyzwań TPM na 2020 rok – piszę w artykule United We Concquer.
- utrwalenie SMED – 31 zespołów wybrało tą metodę redukcji czasów przezbrojeń, z czego prawie 75% prowadziło już wcześniej projekty SMED na tych liniach. Problem polegał na tym, że po początkowych sukcesach po wdrożeniu, kiedy maszyny przejmowali inni pracownicy, a członkowie poprzednich zespołów ds. SMED przechodzili do innych obowiązków, albo po prostu zwalniali się z firmy – czasy przezbrojeń wracały do poziomu wyjściowego. W standardy wkradała się entropia i projekt okazywał się nietrwały.
- zaadaptowanie metody TWI – 25 ekip zdecydowało się popracować nad skróceniem czasu adaptacji nowych pracowników na linie (napiszę osobny artykuł na ten temat – TWI po polsku – okazuje się, że takie jest najskuteczniejsze)
- 10 zespołów – wybrało optymalizację za pomocą KANBAN i poprawę logistyki wewnętrznej,
- a tylko 6 spośród 220 wszystkich zespołów zaangażowanych w 461 optymalizacji wybrało dla siebie udoskonalenie programu wniosków racjonalizatorskich KAIZEN. Nie wiem czemu… albo tak dobrze w tych fabrykach działają, albo po prostu w nie nie wierzą.
35% projektów korzystało z narzędzi problem solving
160 zespołów rozpoczęło projekty, podczas których korzystali z metod znanych z obszaru zarządzania jakością, tj.: 8D, A3, techniki RCA, Pareto, technika 5W+2H czy P i D-FMEA.
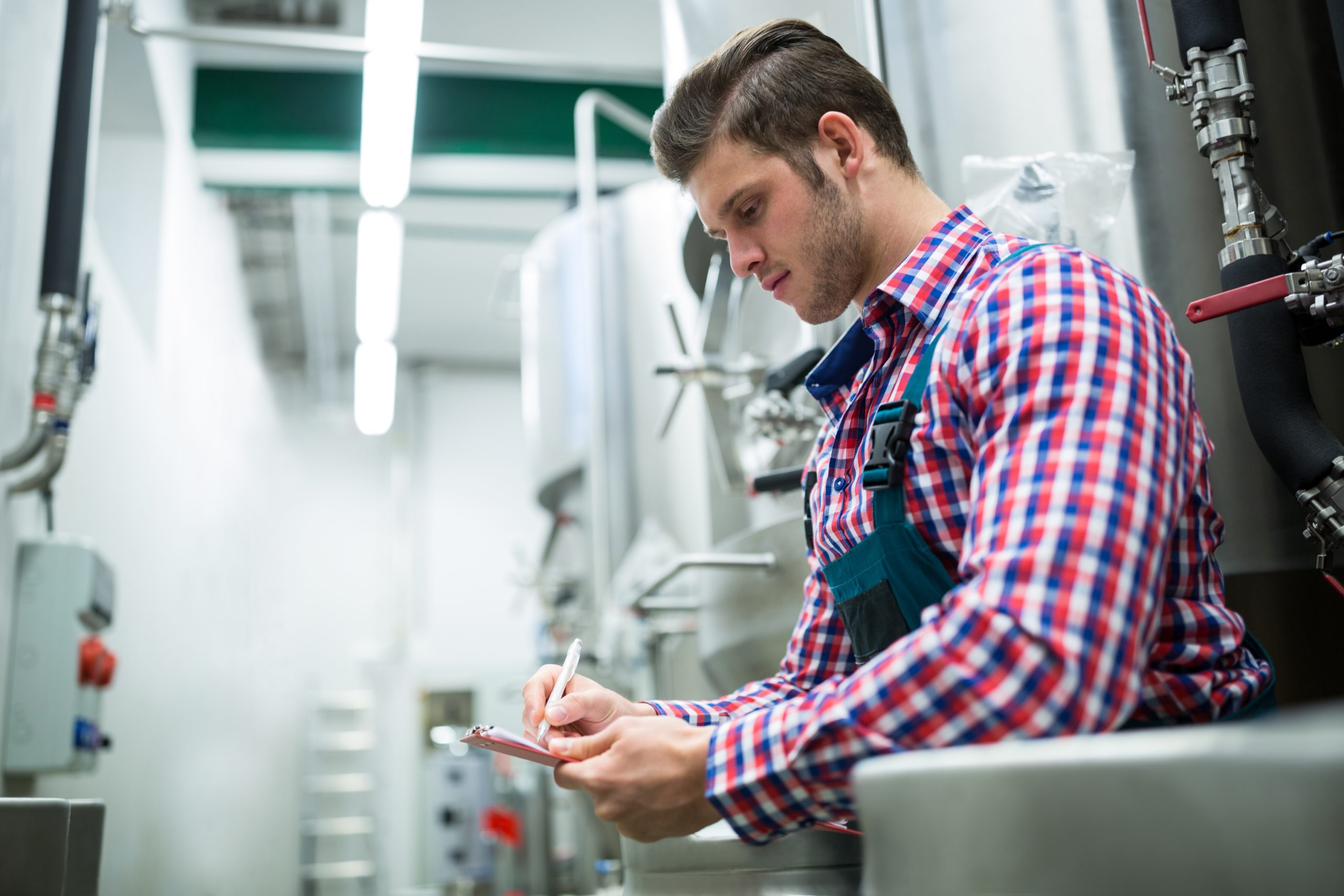
Jakich inicjatyw się podejmowali? (5 tematów)
- poprawa jakości wyrobów – 65 wskazań zespołów (tu nie ma co komentować – temat zawsze na czasie)
- poprawa procesu planowania produkcji, ze szczególnym uwzględnieniem nowych uruchomień projektów, testów jakościowych, aktywności SUR w zakładzie, koordynowania nieplanowanych i planowanych przestojów, wywołań klientów, reklamacji wewnętrznych i zewnętrznych oraz zmian produkcji spowodowanych absencjami pracowników – 40 wskazań;
- lepsza kontrola procesu – 32 zespoły – doszły do wniosku, że zarządzanie stabilnością procesu jest w sumie tańszym sposobem na zapewnienie jakości niż sortowanie detali w poszukiwaniu scrapu przez batalion brakarzy na końcówce linii;
- zapobieganie błędom – 13 zespołów zaangażowało się w projekty FMEA. I mówię tutaj o prawdziwych projektach – nie podróbkach, gdzie działy przerzucają się odpowiedzialnością za zrobienie tabeli, a i tak na tydzień przed audytem VDA siada do niej pełnomocnik lub najbardziej zdesperowany inżynier jakości.
- rozwój dostawców – 10 zespołów, które wykazały, że najlepsze efekty najmniejszym kosztem uzyskają pomagając dostawcą się udoskonalić. Zespoły wskazały kluczowych dostawców i największe problemy z ich dostawami do zakładów, zaplanowały audity procesów tych dostawców, identyfikację przyczyn źródłowych u nich na miejscu i wspólne – partnerskie w formie projekty optymalizacyjne. Cel był prosty – lepszy dostawca to stabilne dostawy, niższe koszty jakości i ograniczone ryzyko zatrzymania linii.
28% tematów skupiło się w obszarze HR
128 zespołów, czyli ponad połowa uruchomiła projekty w obszarze personalnym. Przy założeniu, że ich członkowie to w większości kadra techniczna, jakościowa i produkcyjna, a nie osoby z działów HR – to bardzo wysoki wynik.
To pokazuje jak ważnym tematem optymalizacji są ludzie i to, żeby w tematach jakości, produkcji i utrzymania ruchu się ze sobą dogadywali.
Zespoły wskazały 3 kolejne tematy projektów:
- wzrost motywacji i świadomości załogi – podjęto 59 inicjatyw, które dotyczyły takich tematów jak: zaangażowanie pracowników w rozwój firmy, utrwalanie właściwych postaw na halach produkcyjnych, redukcja negatywnych zachowań i dawanie sobie dobrego przykładu, a także zwiększanie świadomości – np.: obniżanie liczby zwolnień L4 w przypadku gdy pracownicy nie dostawali urlopów na żądanie.
- poprawa współpracy i komunikacji w zespołach – 44 ekipy skoncentrowały swoje wysiłki na poprawie relacji w zespołach i pomiędzy działami, komórkami organizacyjnymi czy zmianami produkcyjnymi. Pewna firma dostrzegły największy potencjał do usprawnień właśnie w obszarze przekazywania zmian. Po wdrożeniu działań zaporowych i utrzymaniu perfekcyjnej organizacji pracy w tym obszarze wydajność linii wzrosła z 36.000 do 41.000 sztuk wyrobów na zmianę.
- w 25 przypadkach rosnący wskaźnik rotacji pracowników. 25 zespołów zaangażowało się w projekty optymalizacje, których celem było ograniczenie kosztów rotacji, które www ich obliczeń potrafiły nawet na prostych stanowiskach pracy wynosić ponad 50.000 / stanowisko. Skąd taki wynik? Oprócz typowych kosztów rekrutacji i adaptacji były to straty spowodowane błędami, kosztami sortowania, resorków, brakowania lub obniżenia wydajności procesu – do czasu osiągnięcia przez nowego pracownika pełnej samodzielności.
Mam nadzieję, że zainspirowałem Cię do działania
Teraz naprawdę Twój ruch. Powołaj zespół i wskaż mu jeden z 14 tematów.
Nawet, gdy Wasza firma jest zamknięta i pracujecie ze sobą zdalnie przez Skype, WhatsUpa, Zooma, Whereby, ClickMeeting, HangOuts od Google czy Microsoft Teams – to akurat tyle ile trzeba, żeby rozpocząć wspólny projekt.
Nalejcie sobie świeży kubek kawy, podzielcie się rolami i zadaniami do wykonania, bo jedyna szansa, żeby nie dać się kryzysowi – to działać.
Powodzenia!